Process Flow of PET Wire Coating Machine


The process flow of PET wire coating machine is a fine and systematic process, which ensures that the surface of PET wire can be uniformly and firmly coated with a layer of functional film. The following is the general process flow of PET wire coating machine:
1、 Preprocessing stage
Wire preparation: Firstly, it is necessary to prepare PET wire to ensure that its surface is clean, free of scratches, oil stains, etc.
Cleaning treatment: Use appropriate cleaning agents to clean the PET wire, removing surface grease, dust, and other pollutants. During the cleaning process, attention should be paid to controlling the temperature and concentration of the cleaning solution, as well as the cleaning time, to avoid damage to the wire.
Drying treatment: The cleaned PET wire needs to be dried to remove residual moisture and cleaning agents. The drying temperature and time need to be determined according to the material and coating requirements of the wire.
2、 Coating stage
Preparation of coating solution: Prepare the coating solution according to the required functional coating. The composition, concentration, viscosity, and other parameters of the coating solution need to be determined according to specific coating requirements.
Coating operation: The PET wire is fed into the coating machine, and the coating liquid is evenly coated on the surface of the wire through the coating head or coating roller. During the coating process, it is necessary to control parameters such as coating speed, coating amount, and coating temperature to ensure the uniformity and stability of the coating.
Pre curing treatment: After coating is completed, it may be necessary to preheat the wire to improve the curing efficiency and adhesion of the coating.
3、 Curing stage
Curing treatment: The coated PET wire is sent to a curing furnace for heating treatment, causing a chemical reaction in the coating material to form a strong coating. The curing temperature and time need to be determined according to the material and requirements of the coating.
Cooling treatment: After curing is completed, the wire needs to be cooled to avoid problems such as wire deformation or coating cracking caused by high temperature.
4、 Post processing stage
Inspection and testing: Inspect and test the coated PET wire, including visual inspection, coating thickness measurement, adhesion testing, etc., to ensure that the coating quality and performance meet the requirements.
Roll up and packaging: Roll up and package PET wires that have passed inspection for subsequent storage and transportation.
5、 Quality control
Throughout the entire process, it is necessary to strictly control the quality of each link, including the quality of raw materials, coating liquid, coating process stability, and control of curing conditions. At the same time, regular quality testing and evaluation of finished products are also required to ensure consistency and stability of product quality.
Qingdao Chenan Machinery Co., Ltd. has the advantage of developing and producing rubber winding equipment, with higher technology than various equipment assembly manufacturers in the industry. For more information about PET wire coating machine, please contact us.
Company: Qingdao Chenan Machinery Co., Ltd.
Address: Yanjialing Industrial Park, East Chengma Road, Tongji New Economic Zone, Jimo District, Qingdao City, Shandong Province
Email: qdcajx@gmail.com
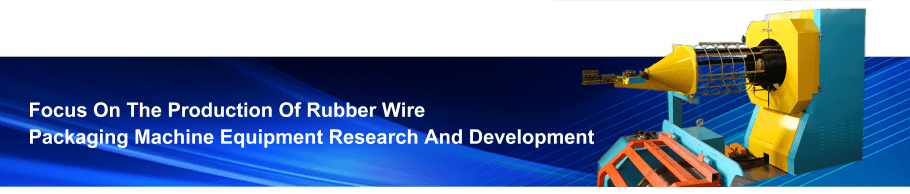
Recommended
04-17What is the Market Prospect of PET Coated Wire Ropes
04-16Can Nylon Coated Steel Wire be Used in Life
04-10What are the Disadvantages of White PET Coated Wire
04-09Processing Performance of Nylon Coated Wire
04-03What are the Main Applications of PET Coated Binding Wire
04-02Insulation Performance Characteristics of Nylon Coated Wire