Quality Standards for PET Coated Wire


The quality standards of PET coated wires cover many aspects such as materials, structure, performance, and environmental protection. These standards ensure the safety, reliability, and stability of wires in electrical systems. In practical applications, appropriate PET coated wires should be selected according to the specific use environment and requirements.
1. Material standards
Conductor materials: The conductors of PET coated wires are usually made of metal materials such as copper or aluminum, which should have good conductivity and mechanical strength.
Insulation materials: PET materials, as insulating layers, should meet specific electrical insulation performance requirements, such as dielectric strength, insulation resistance, etc. At the same time, PET materials should also have good heat resistance, wear resistance, and chemical corrosion resistance.
2. Structural standards
Coating structure: The PET coating should be tightly and evenly coated on the surface of the conductor without defects such as bubbles, cracks, and peeling.
Conductor structure: The conductor should be in a regular geometric shape, such as round, flat, etc., and the dimensional tolerance should meet relevant standards.
3. Performance standards
Electrical performance: PET coated wires should meet specific electrical performance requirements, such as rated voltage, rated current, insulation resistance, dielectric strength, etc. These performance parameters determine the safety and reliability of wires in electrical systems.
Mechanical properties: The wires should be able to withstand certain mechanical stresses such as tension, pressure, bending, etc. without damage such as breakage and deformation.
Heat resistance: PET coated wires should be able to operate stably for a long time in a specified high temperature environment without performance degradation or damage.
Chemical corrosion resistance: The wires should be able to resist the erosion of chemical substances such as acids, alkalis, and salts, and maintain the stability of their electrical and mechanical properties.
4. Environmental protection standards
PET coated wires should meet relevant environmental protection requirements, such as non-toxic, odorless, and pollution-free. During production and use, the negative impact on the environment should be minimized.
5. Other standards
Marking and packaging: The surface of the wire should be clearly and accurately marked with information such as model, specification, manufacturer, etc. The packaging should be firm, moisture-proof, and damage-proof to ensure the safety of the wires during transportation and storage.
Test methods: When testing the various performance indicators of PET coated wires, specific test methods and standards should be followed to ensure the accuracy and reliability of the test results.
Qingdao Chenan Machinery Co., Ltd. has the advantage of developing and producing rubber winding equipment, with higher technology than various equipment assembly manufacturers in the industry. For more information PET coated wire, please contact us.
Company: Qingdao Chenan Machinery Co., Ltd.
Address: Yanjialing Industrial Park, East Chengma Road, Tongji New Economic Zone, Jimo District, Qingdao City, Shandong Province
Email: qdcajx@gmail.com
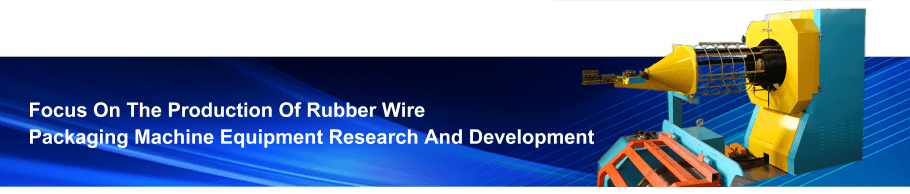
Recommended
04-17What is the Market Prospect of PET Coated Wire Ropes
04-16Can Nylon Coated Steel Wire be Used in Life
04-10What are the Disadvantages of White PET Coated Wire
04-09Processing Performance of Nylon Coated Wire
04-03What are the Main Applications of PET Coated Binding Wire
04-02Insulation Performance Characteristics of Nylon Coated Wire