What are the Disadvantages of PET Coated Steel Wire


PET coated steel wire, as a composite product that combines the strength of steel wire and the excellent properties of PET material, although widely used in multiple fields, also has some drawbacks. The following is a detailed analysis of the drawbacks of PET coated steel wire:
1. Coating adhesion issue
Problem description: The adhesion between PET coating and steel wire substrate is one of the key factors affecting the performance of coated steel wire. If the adhesion is insufficient, the coating is prone to peeling and flaking during use, which affects the overall performance and lifespan of the product.
Possible reasons: Insufficient adhesion may be related to factors such as coating process, material selection, and substrate surface treatment. For example, improper control of temperature, pressure, and other parameters during the coating process, or insufficient cleaning and pretreatment of the substrate surface, can all lead to poor adhesion.
2. Weather resistance limitations
Problem description: Although PET material itself has certain weather resistance, the performance of PET coating may be affected under extreme environmental conditions (such as extreme high temperature, low temperature, strong ultraviolet radiation, etc.), resulting in aging, discoloration, cracking and other problems.
Scope of impact: This may lead to a decrease in the anti-corrosion, wear-resistant and other properties of coated steel wire, shortening the service life of the product.
3. Processing performance limitations
Problem description: The processing performance of PET coated steel wire may be affected by factors such as coating thickness and hardness. Excessive thickness or hardness of the coating may increase processing difficulty, affecting the forming accuracy and surface quality of the product.
Solution suggestion: In the design and production process, it is necessary to fully consider the requirements of processing performance, choose appropriate coating thickness and hardness, and adopt suitable processing technology and equipment.
4. Cost considerations
Problem description: Compared to uncoated steel wire, the production cost of PET coated steel wire may increase. This is mainly due to factors such as coating process, material cost, and processing difficulty.
Economic impact: Increased costs may affect the market competitiveness and profit margins of products, requiring companies to weigh and consider them in their production decisions.
5. Environmental issues
Problem description: Although PET material itself is a recyclable and environmentally friendly material, there may be certain waste and pollution generated during the production and use of coated steel wire. For example, the exhaust gas and wastewater that may be generated during the coating process need to be properly treated.
Solution suggestion: Enterprises should strengthen their environmental awareness, adopt environmentally friendly production processes and equipment, and reduce the generation of waste and pollution. At the same time, actively promote the recycling and reuse of waste coated steel wire to achieve the circular utilization of resources.
Qingdao Chenan Machinery Co., Ltd. has the advantage of developing and producing rubber winding equipment, with higher technology than various equipment assembly manufacturers in the industry. For more information about PET coated steel wire, please contact us.
Company: Qingdao Chenan Machinery Co., Ltd.
Address: Yanjialing Industrial Park, East Chengma Road, Tongji New Economic Zone, Jimo District, Qingdao City, Shandong Province
Email: qdcajx@gmail.com
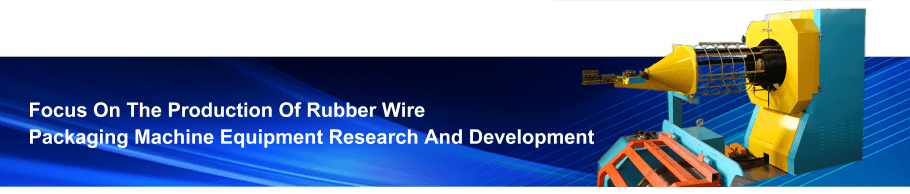
Recommended
07-17What are the Advantages of PET Coated Galvanized Wire
07-16Selection Criteria for Nylon Coated Wire Supplier
07-10Key Features of White PET Coated Wire
07-09How to Evaluate the Customization Capabilities of Nylon Coated Wire Factories
07-03Environmental Friendliness of Black PET Coated Wire
07-02Characteristics of Professional Nylon Coated Wire Manufacturer