What should be Paid Attention to When Replacing PE Coating Machine Parts


When replacing PE coating machine parts, it is necessary to focus on safety isolation, standardized operation, component adaptability, use of professional tools and equipment debugging. The following are specific precautions:
1. Safety isolation and shutdown specifications
Power off and hang up: Before replacing parts, the main power supply of the equipment must be cut off, and a "no closing" warning sign must be hung on the control box to prevent accidental start-up. For parts involving hydraulic or pneumatic systems, the air source must be turned off and the residual pressure must be released simultaneously.
Equipment cooling: For high-temperature parts (such as heat sealing rollers and heating modules), the temperature must drop below 40°C before operation to avoid burns or fire.
Lock protective devices: Before disassembly, ensure that safety doors, protective covers and other devices are locked to prevent accidental movement of the equipment.
2. Component disassembly and installation specifications
Special tool use: Precision parts such as coating heads and scrapers require special disassembly tools to avoid deformation caused by violent disassembly and assembly. Bolt disassembly is carried out in diagonal order to prevent unilateral force from damaging the thread.
Component cleaning and inspection: Immediately clean the residual glue and dust on the surface of the component after disassembly, and check whether the sealing surface is flat and has no scratches. Flexible parts such as rubber rollers and conveyor belts need to be checked for cracks, aging or permanent deformation.
Installation accuracy control: A laser rangefinder is required to adjust the gap between the coating head and the substrate, and the error is controlled within ±0.01mm. After the conveyor belt is installed, the deviation amount needs to be detected by a dynamic balancer to ensure that it is ≤1mm/m.
Lubrication and corrosion protection: Apply special grease to moving parts such as bearings and gears before reinstallation to prevent direct metal contact. Exposed metal parts need to be coated with anti-rust oil to avoid rust caused by long-term downtime.
3. Component compatibility verification
Model matching: The model and specifications of the replaced parts must be consistent with the original equipment, such as the coating head width must match the substrate width. Imported equipment needs to confirm whether the spare parts have passed the original factory certification to avoid using third-party accessories with poor compatibility.
Parameter calibration: After replacement, the coating speed, temperature, pressure and other parameters need to be reset, and the no-load test run is carried out for 30 minutes. The coating thickness uniformity is tested by an X-ray thickness gauge, and the CV value must be ≤1.5%.
Compatibility test: New parts need to be tested for compatibility with existing glue and substrates to observe coating adhesion and bubble generation.
4. Professional personnel and process management
Personnel qualifications: Operators must hold maintenance qualifications certified by the equipment manufacturer, or pass the company's internal special training assessment. Operations involving electrical and hydraulic systems must be completed by certified electricians and fitters.
Standardized process: Before replacement, you need to fill in the "Equipment Maintenance Application Form" to specify the name, reason, and estimated time of the replacement part. After replacement, fill in the "Equipment Maintenance Record Form" to record the replacement time, parameter adjustment, and trial run results.
Spare parts management: Establish a safety inventory of key parts (such as 2 sets of coating heads and 3 conveyor belts), and check the status of spare parts regularly. Spare parts must be stored by model and batch to avoid mixing or expiration.
5. Emergency handling and subsequent verification
Abnormal situation handling: If the equipment has abnormal noise or vibration exceeds the standard after replacement, it is necessary to stop the machine immediately to check whether the component installation is loose. When the coating quality does not meet the standard, it is necessary to trace back to check the cleanliness, installation accuracy and parameter settings of the components.
Long-term tracking: Equipment inspections must be strengthened within 72 hours after replacement, with a focus on monitoring the operating status of the replaced parts. The failure rate and service life of the replaced parts are counted monthly to optimize spare parts procurement plans.
Qingdao Chenan Machinery Co., Ltd. has the advantage of developing and producing rubber winding equipment, with higher technology than various equipment assembly manufacturers in the industry. For more information about pe coating machine, please contact us.
Company: Qingdao Chenan Machinery Co., Ltd.
Address: Yanjialing Industrial Park, East Chengma Road, Tongji New Economic Zone, Jimo District, Qingdao City, Shandong Province
Email: qdcajx@gmail.com
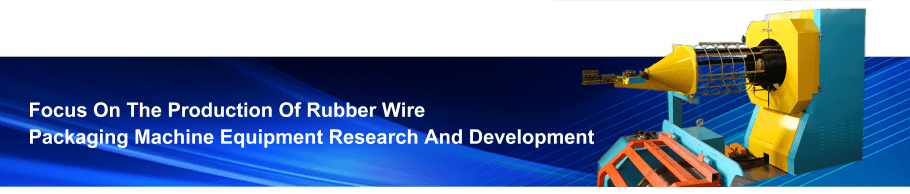
Recommended
04-29Will the Insulation of Nylon Covered Wire be Affected by the Environment?
04-24How to Choose a PET Coated Wire Factory
04-23Application of Nylon Coated Wire in the Electronics Field
04-17What is the Market Prospect of PET Coated Wire Ropes
04-16Can Nylon Coated Steel Wire be Used in Life
04-10What are the Disadvantages of White PET Coated Wire