Application Areas of DLC Coating Machine


The application fields of DLC coating machines are very wide, mainly due to the excellent properties of DLC coatings such as high hardness, wear resistance, chemical stability, and low friction. The following are some of the main application areas of DLC coating machines:
1. Mechanical Engineering:
Tools and molds: DLC coating can significantly improve the wear resistance of tools and molds, extend their service life, reduce cutting force and frictional heat, thereby improving machining efficiency and quality.
Bearings and sliding components: DLC coating can reduce friction coefficient, decrease wear, and improve the reliability and durability of bearings and sliding components.
Automotive components such as engine parts, brake systems, transmission systems, etc., DLC coatings can enhance their wear resistance, corrosion resistance, and thermal fatigue resistance.
2. Electronics and semiconductor industry:
Hard disk read-write head: DLC coating is widely used as a protective coating for hard disk read-write heads due to its low friction and high wear resistance, improving read-write speed and stability.
Microelectronic components: DLC coating can be used to protect the surface of microelectronic components, prevent chemical corrosion and mechanical wear, and improve the reliability and lifespan of the components.
3. Biomedical:
Medical devices: DLC coatings are used in medical devices such as surgical knives, bone screws, joint replacements, etc. to improve their biocompatibility, wear resistance, and corrosion resistance.
Dental materials: DLC coating can improve the surface performance of dental implants and tools such as dental drills, enhancing their effectiveness.
4. Optics and Optical Instruments:
Optical lenses: DLC coating can be used to protect optical lenses, improve their scratch resistance and wear resistance, while maintaining high transmittance.
Laser equipment: DLC coating can be used for the mirrors and lenses of laser equipment to improve reflectivity and transmittance, reduce thermal effects and light damage.
5. Aerospace:
Engine components: DLC coating can be used for components in high-temperature and high-pressure environments such as aircraft engines to improve their wear resistance, corrosion resistance, and thermal fatigue resistance.
Space equipment: DLC coating can be used for surface protection of space equipment, resisting the effects of cosmic radiation and extreme temperature environments.
6. Sports equipment:
Golf Club: DLC coating can improve the wear resistance and hardness of golf clubs, extend their service life, and enhance the hitting effect.
Skies and skateboards: DLC coating can reduce sliding resistance, improve sliding speed and smoothness.
Qingdao Chenan Machinery Co., Ltd. has the advantage of developing and producing rubber winding equipment, with higher technology than various equipment assembly manufacturers in the industry. For more information about dlc coating machine, please contact us.
Company: Qingdao Chenan Machinery Co., Ltd.
Address: Yanjialing Industrial Park, East Chengma Road, Tongji New Economic Zone, Jimo District, Qingdao City, Shandong Province
Email: qdcajx@gmail.com
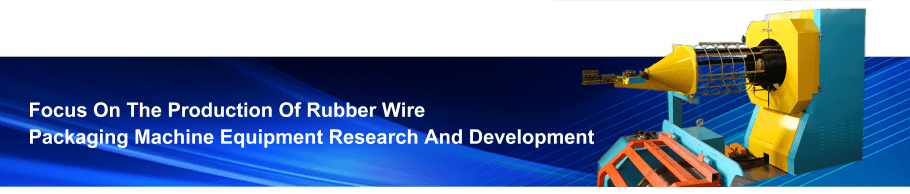
Recommended
04-16Can Nylon Coated Steel Wire be Used in Life
04-10What are the Disadvantages of White PET Coated Wire
04-09Processing Performance of Nylon Coated Wire
04-03What are the Main Applications of PET Coated Binding Wire
04-02Insulation Performance Characteristics of Nylon Coated Wire
03-27How to PET Coated Wires for Sale Better