What is the Daily Maintenance Cycle for Chrome Coating Machines?


The maintenance cycle of different components of the chrome coating machine varies due to factors such as frequency of use and working environment
1. Daily maintenance
Plating tank: After each use, the chromium slag on the surface of the plating tank should be cleaned to avoid the accumulation of chromium slag affecting the chrome coating effect. At the same time, check the liquid level of the chrome coating solution to ensure that it can submerge the workpiece and electrode. If the liquid level is too low, it is necessary to replenish the chrome coating solution in a timely manner.
Electrode: Check whether the connection between the cathode (workpiece fixture) and the negative pole of the power supply is firm, as well as the connection between the anode and the positive pole of the power supply. Check whether there are signs of looseness, corrosion, etc. at the connection point.
Power system: Before starting up, check the appearance of the power equipment, including whether the casing is damaged and whether the indicator lights are working properly. At the same time, check if the cooling fan is running properly to ensure that the power supply can effectively dissipate heat during operation.
2. Weekly maintenance
Plating tank: Check the basic properties such as color and transparency of the chrome coating solution to preliminarily determine whether the solution has been contaminated. If the color of the solution is abnormal (such as turning black or cloudy) or if there is an odor, it may indicate that there are too many impurities in the solution and further analysis and treatment are needed. At the same time, check the filter element of the filtration device. If blockage is found, it should be replaced in a timely manner to ensure the filtration effect of the solution.
Electrode: Check if there is chrome coating deposition on the surface of the cathode fixture. If there is slight deposition, use sandpaper or other tools for simple cleaning. At the same time, check whether the wires of the cathode and anode are damaged, aged, etc., to ensure normal current transmission.
Power supply system: Use simple tools such as voltmeter and ammeter to check whether the output voltage and current of the power supply are within the normal range, ensuring the stability of the power output. If any deviation is found, further inspection and calibration are required.
Mixing device: For mechanical mixing devices, check whether the mixing blade is loose and whether there is abnormal noise during motor operation; For the air mixing device, check for any signs of blockage in the air nozzle. If there is a slight blockage, perform a simple cleaning.
3. Monthly maintenance
Plating tank: Conduct a thorough cleaning of the plating tank, using a mild acidic cleaner to clean the tank walls and bottom, and then rinse thoroughly with plenty of water to ensure that there are no residual cleaning agents. At the same time, chemical analysis is conducted on the chrome coating solution to accurately measure the concentrations of major components such as chromic acid and sulfuric acid, and adjust the solution composition based on the analysis results.
Electrode: Conduct a detailed inspection of the anode. If there is corrosion or passivation on the surface of the anode, such as the appearance of an oxide layer, it can be soaked and cleaned with a dilute nitric acid solution. At the same time, a deeper cleaning of the cathode fixture may be necessary, and if the chromium plating layer is thick, a plating solution may need to be used for treatment.
Power system: Clean the interior of power equipment, remove dust and other impurities, and avoid the accumulation of dust affecting heat dissipation or causing electrical failures. At the same time, check whether the protection functions of the power supply, such as overload protection, short circuit protection, etc., are normal, which can be tested by simulating simple fault situations.
Mixing device: For mechanical mixing devices, check the degree of wear of the mixing blades. If the wear is severe, consider replacing them; For the air mixing device, clean the air filter to ensure its normal operation and prevent impurities from entering the compressed air pipeline.
Temperature control system: Check whether the wiring of the heating device is secure, and at the same time check whether the heating rod (if it is an electric heating rod) has any abnormal conditions such as local overheating or discoloration. Check if the probe of the temperature sensor is clean and if the temperature measurement is accurate. If there is any deviation, calibration is required.
4. Quarterly maintenance
Plating tank: Check the corrosion resistance of the plating tank, especially the part of the tank body in contact with the solution, to see if there are any signs of corrosion. If corrosion is found, timely measures should be taken to repair or replace the plating tank components.
Electrode: Conduct a comprehensive evaluation of the performance of the electrode, including the conductivity of the anode and the contact resistance of the cathode fixture. If there is a significant decrease in electrode performance, it is necessary to consider replacing the electrode or carrying out repair treatment.
Power system: Please have professional personnel conduct comprehensive performance testing and calibration of the power supply, including voltage accuracy, current accuracy, ripple coefficient and other parameters, to ensure that the power system can meet the working requirements of the chrome coating machine.
Temperature control system: Calibrate the temperature sensor to ensure its measurement accuracy is within a reasonable range. Standard thermometers and temperature sensors can be used to measure the temperature of the solution simultaneously, compare the measurement results, and make adjustments.
5. Maintenance every six months to one year
Plating tank: Change the chrome coating solution in a timely manner according to the usage of the plating tank and the solution replacement cycle. At the same time, conduct a comprehensive inspection and maintenance of the ancillary equipment of the plating tank, such as the solution circulation system and the replenishment system, to ensure their normal operation.
Electrode: Consider replacing the anode (if the lifespan of the anode is approaching its limit) to ensure its performance. At the same time, conduct a comprehensive inspection and maintenance of the cathode fixture, including replacing severely worn fixture components, updating the insulation materials of the fixture, etc.
Power system: Check the performance and lifespan of the main electrical components of the power system, such as capacitors, transformers, etc., and replace or maintain them as needed. At the same time, inspect the wiring of the power system to ensure the safety and reliability of the circuit.
Mixing device: For mechanical mixing devices, consider replacing vulnerable components such as bearings of the mixing motor; For the air mixing device, check and replace the aging parts of the compressed air pipeline to ensure the sealing and safety of the pipeline.
Temperature control system: Comprehensive maintenance of heating devices, such as descaling or replacement of electric heating rods; For steam heating tubes, check for any leaks or other issues. At the same time, check the control instruments of the temperature control system, such as temperature controllers, to ensure their accuracy and reliability.
Qingdao Chenan Machinery Co., Ltd. has the advantage of developing and producing rubber winding equipment, with higher technology than various equipment assembly manufacturers in the industry. For more information about chrome coating machine, please contact us.
Company: Qingdao Chenan Machinery Co., Ltd.
Address: Yanjialing Industrial Park, East Chengma Road, Tongji New Economic Zone, Jimo District, Qingdao City, Shandong Province
Email: qdcajx@gmail.com
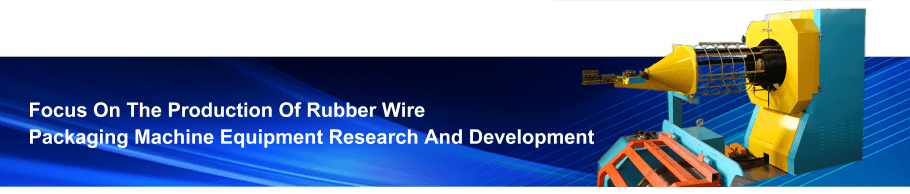
Recommended
07-03Environmental Friendliness of Black PET Coated Wire
07-02Characteristics of Professional Nylon Coated Wire Manufacturer
06-26Safety Performance of PET Coated Wire Rope
06-25How to Choose Black Nylon Coated Wire
06-19Material Properties of PET Coated Iron Wire
06-18Performance Advantages of 1 4 Nylon Coated Wire